新HCPによる次世代デバイスの加工接着技術
【特許出願中】
背景
LEDなどの製作工程として基板の裏面加工を行います。その際、ワークをプレートに接着し、加工します。
厚さバラつきを抑えた高精度の製品を製作するにはワックス層の均一な高精度の接着が必須です。
しかし、この時のワークは下記のような特徴があり、高精度の接着が困難です。
ワークの特徴
- 剛性が高い
- そりが大きい
- 少量生産のため厚さが揃っていない
課題
- 剛性が高く、そりが大きい加工物の場合は、従来のヒーターと冷却が別のシステムではワークのそりを矯正出来ずに冷却が進み、ワックスが固化するため、ワックス層を均一に接着することが困難です。
- 従来の一括式プレス方法では厚さの異なったワークを同一プレートに接着するとワックス層に厚さムラが生じます。
従来の接着イメージ動画
新HCPの特徴
- 同一ステージで加温&加圧そして冷却が可能
ワックスが高温で完全に軟化している状態で加圧し、ワークのそりを矯正し、ワックス層を均一に延ばした状態で加温から冷却に切り替えることで均一な厚さのワックス層が得られます。
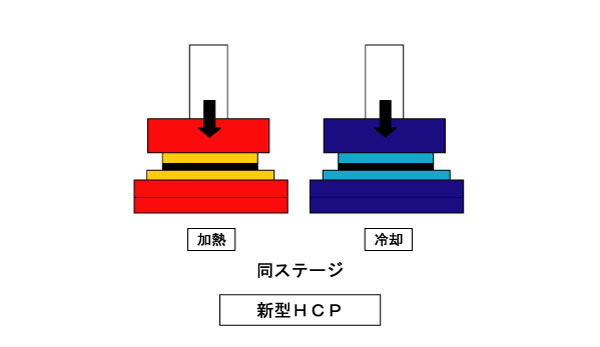
新型機の接着イメージ動画
- 分割式プレスヘッドを搭載
ワーク一枚一枚を個別のヘッドで加圧することによって、隣接のワークとの厚さ差の影響を受けることなくワーク全面に圧力を加えることが出来るので、ワックス層を均一に延ばすことが出来ます。
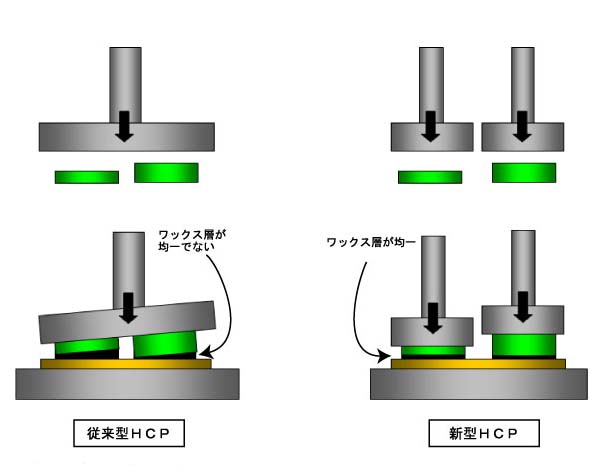
一括式イメージ動画 分割式イメージ動画